Food safety is a design priority – PR News Blog
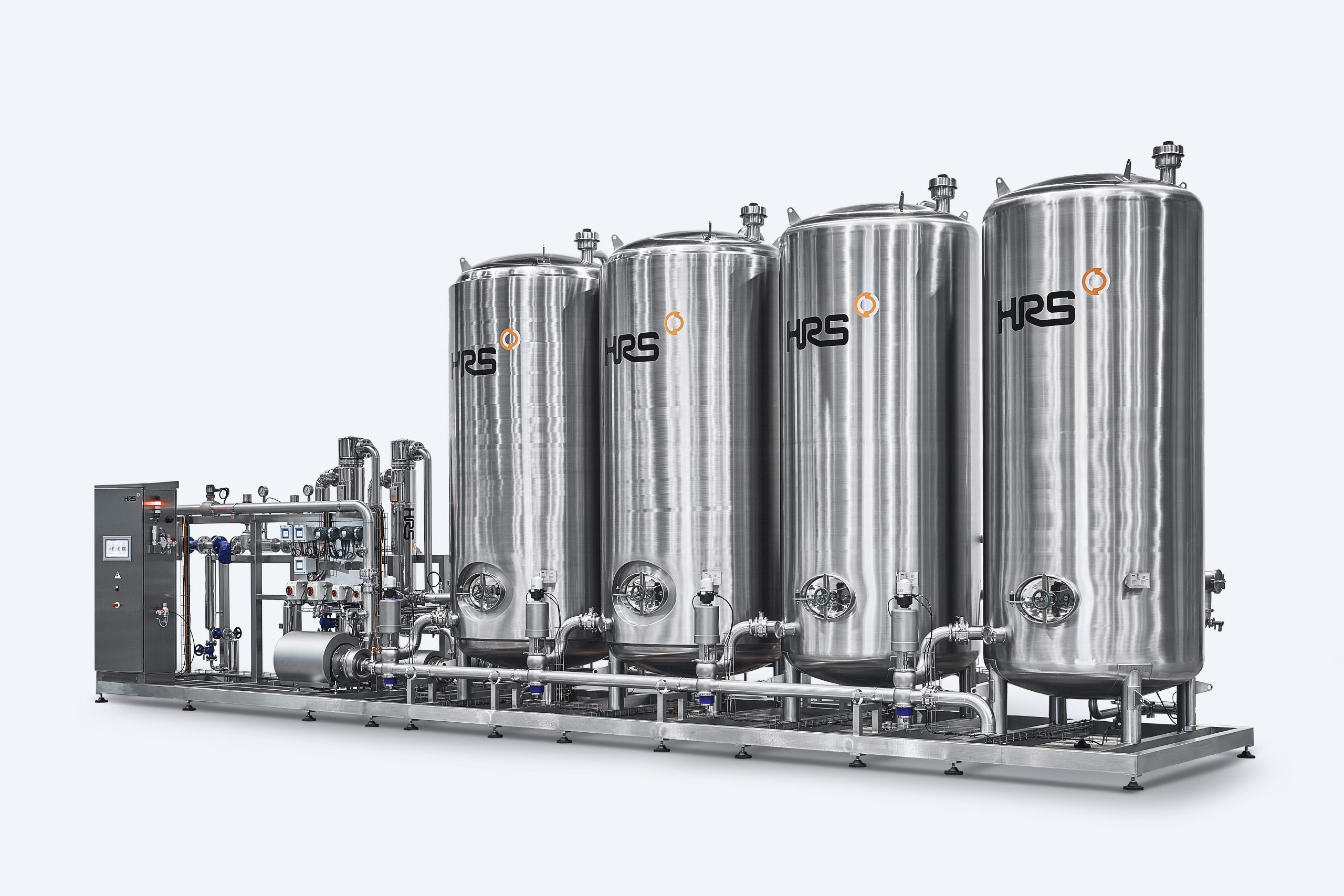
By Matt Hale, International Sales and Marketing Director, HRS Heat Exchangers
Modern food production systems have reduced the cost of food and made it more available, but general trends towards centralization of food supply also increase the possibility that food safety issues, such as contamination with pathogens or toxins, affect a large number of people.1. To prevent this, food producers implement strict systems such as Hazard Analysis and Critical Control Points (HACCP), but design and manufacturing standards for food processing equipment are also of importance. vital.
Kinds of pollution
Contamination of food and beverage products can lead to minor quality issues, serious health issues and even death. There are four main types of contamination that can affect food and beverage products: microbial, chemical, physical and allergenic.
Microbial contamination is caused by microorganisms such as bacteria, viruses, molds, fungi and toxins such as campylobacter, salmonella and E.coli, and microbial contamination is the most common source of food poisoning. Control measures include strict hygiene measures, ensuring the separation between raw and cooked ingredients, and the use of techniques to reduce the microbial load in the product, such as pasteurization or sterilization.
Chemical contamination often comes from poor control of the products used for cleaning and disinfection. If chemical residues remain on food preparation or contact surfaces, or if chemicals are used near food and beverage products, contamination may occur. Another source of chemical contamination can be the production of primary food ingredients such as the incorrect use of pesticides and drugs on farms.
As the name suggests, physical contamination is caused by foreign bodies and can include anything from stones and harmful bodies to plastic or metal objects. In food processing facilities, poorly maintained or poorly designed equipment can itself become a source of physical contamination in the form of things like peeling paint or loose screws. Physical contaminants can also carry harmful bacteria, increasing the overall risk of contamination.
The final source of contamination is allergen contamination, which occurs when a food that causes an allergic reaction comes into contact with another food. There are 14 recognized allergens2including gluten, peanuts, eggs, mustard, soy, and fish, and the reactions caused can range from mild discomfort to life-threatening anaphylactic shock.
The importance of design
Food processing companies adopt a range of processes and procedures to prevent these forms of contamination from occurring. These measures may include cleaning and maintenance procedures, pest control, personal hygiene, protective clothing, dress codes, etc. Many of these procedures will have been implemented as a result of the Hazard Critical Control Point (HACCP) assessment of the facility and production. methods employed, but there is another equally important aspect to avoiding contamination that is not always highlighted: the design and construction of the food processing equipment itself.
The hygienic design of the equipment improves cleanability, reducing the risk of biological, physical and chemical contamination. In addition, equipment designed and constructed to meet hygienic principles is easier to maintain and reduces the risk of physical hazards.3.
Hygienic design principles encompass a range of different factors, including the choice of materials, surface finish and methods of construction, as well as the physical design of the product – for example avoiding lips, crevices and sharp corners where cleaning chemicals or product may accumulate or remain after cleaning. To facilitate cleaning under and around the equipment, it should be raised off the ground on feet or mounted in a frame (as is the case with HRS skid mounted systems).
When designing equipment, different standards may be applied to food contact and non-contact surfaces, and surfaces that come into contact with product should generally be smooth, non-toxic, non-absorbent, and corrosion-resistant. For this reason, stainless steel is a popular choice and AISI 300 series stainless steel (as specified by 3A sanitary standards) is used as a key material by HRS heat exchangers. Welding and joints are also important; continuous butt welds should be used and ground to a smooth surface, while bolts and threads used in the food contact area should be of hygienic design.
It is also important to maintain the movement of fluids and materials within the equipment and connecting piping. Maintaining flow and preventing fouling is also a key priority in heat exchanger design and that is why HRS heat exchangers produce corrugated tube or scraped surface designs. It is also important to use closed coupled connections to the equipment to avoid the creation of dead spots and to ensure that, if necessary, the equipment can be fully drained or emptied for cleaning or change of product. Other considerations include avoiding the use of o-rings in the grooves, avoiding ledges around the top flanges, and ensuring shafts are properly sealed with double seals if necessary.
Reduce waste while maintaining safety
HRS Heat Exchangers produce a wide range of equipment for the food and beverage industry, from basic tubular heat exchangers to fully integrated pasteurization/sterilization and aseptic filling systems, as well as a number of specialist products such as evaporators, ice crushers and melters. , direct steam injection systems, exhaust air systems and pumps. All of these are hygienically designed from the start to facilitate clean operation and avoid the types of product contamination discussed above. All HRS products designed for food use meet 3A sanitary standards.
In addition, HRS equipment is specially designed to facilitate product evacuation and subsequent cleaning. It has always been a challenge for food and beverage companies to implement effective and rigorous CIP regimes that meet the necessary standards in a way that minimizes the loss or degradation of salable or useful products. An example is the HRS R series of rotary scraped surface heat exchangers which can physically remove product without the need for traditional scraping or rinsing systems.
The R-Series is suitable for a range of heat transfer applications and its unique design allows high viscosity products to be pumped with reduced back pressure and energy consumption. The helical spiral is equipped with scrapers – which scrape the surface of the tubes to prevent clogging in normal use – can also work in reverse; allowing valuable product to be recovered before routine cleaning or product changeover. This design feature means that much of the product can be removed from the HRS R series without the need for additional pumps or pressure systems, reducing both CAPEX and OPEX.
HRS also produces a product recovery system, which combines continuous monitoring of a defined parameter (eg Brix, pH or viscosity) with the three-way valve technology used in every HRS pasteurizer or sterilizer. Working together, these two systems ensure that all product that meets defined parameters is used and only that which falls outside (for example, that diluted before or during CIP) is discarded. Additionally, such monitoring helps validate the effectiveness of CIP and ensures that after a cleaning cycle, only product that meets specifications is allowed to continue.
The hygienic design and construction of food processing equipment is an essential but often overlooked aspect of food and beverage safety and quality control, playing a crucial role in preventing contamination and enabling the implement other food safety procedures.